From Nature to Innovation
At TypeOne Biomaterials, we transform Type I collagen – a protein of extraordinary biological relevance – into high-performance materials for medical and regenerative applications.
Sourcing & Raw Collagen Extraction
Extraction is performed using proprietary methods that preserve the native triple-helix structure of collagen—a critical factor for its bioactivity. Through controlled enzymatic digestion and purification, we remove non-collagenous proteins, fats, and other impurities while maintaining the molecular integrity of the collagen fibers.
Collagen Purification
and Stabilization
Production of Semi-Finished
Collagen Materials
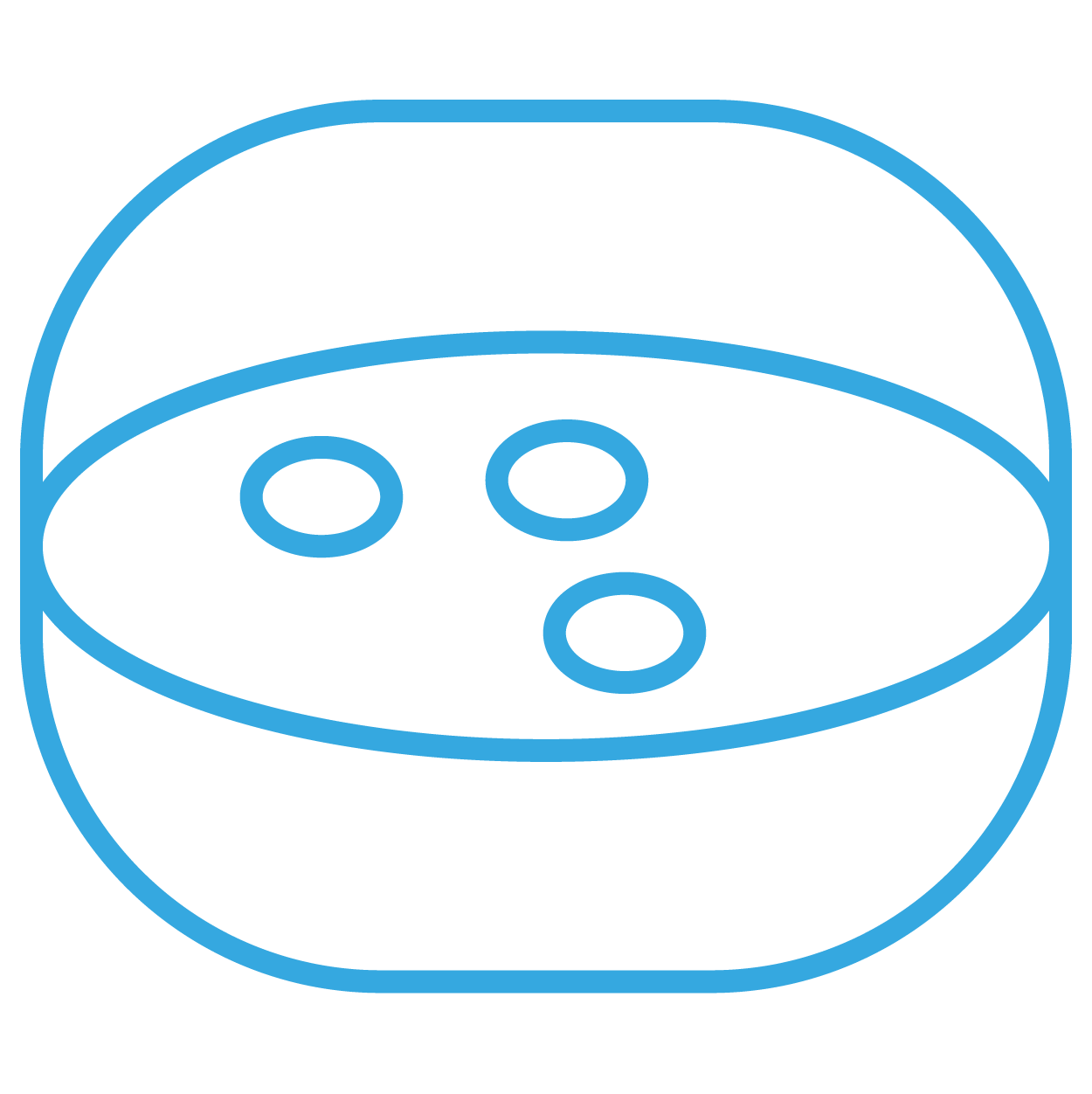
Membranes
for wound healing and surgical applications
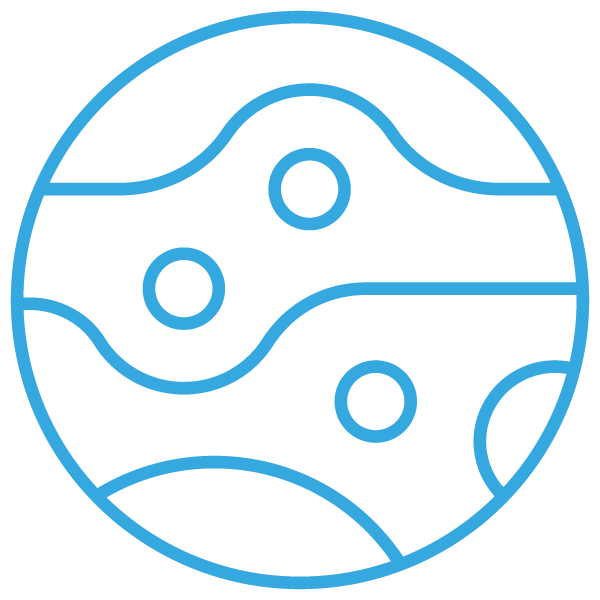
Sponges and matrices
for tissue regeneration and 3D scaffolding
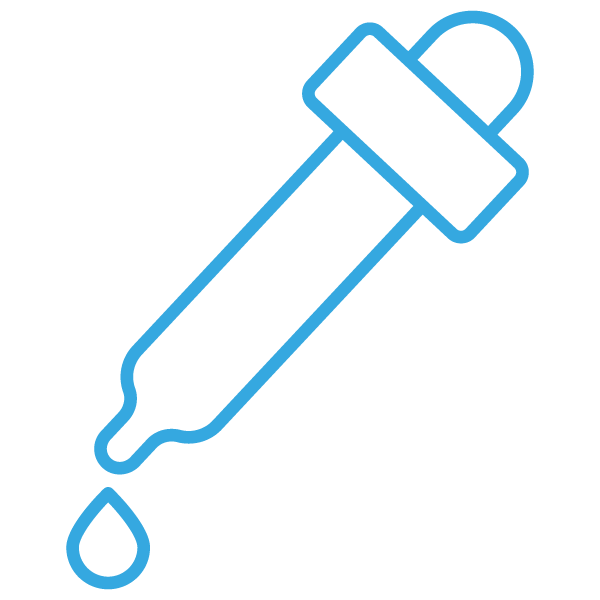
Injectable gels
for aesthetic and regenerative medicine
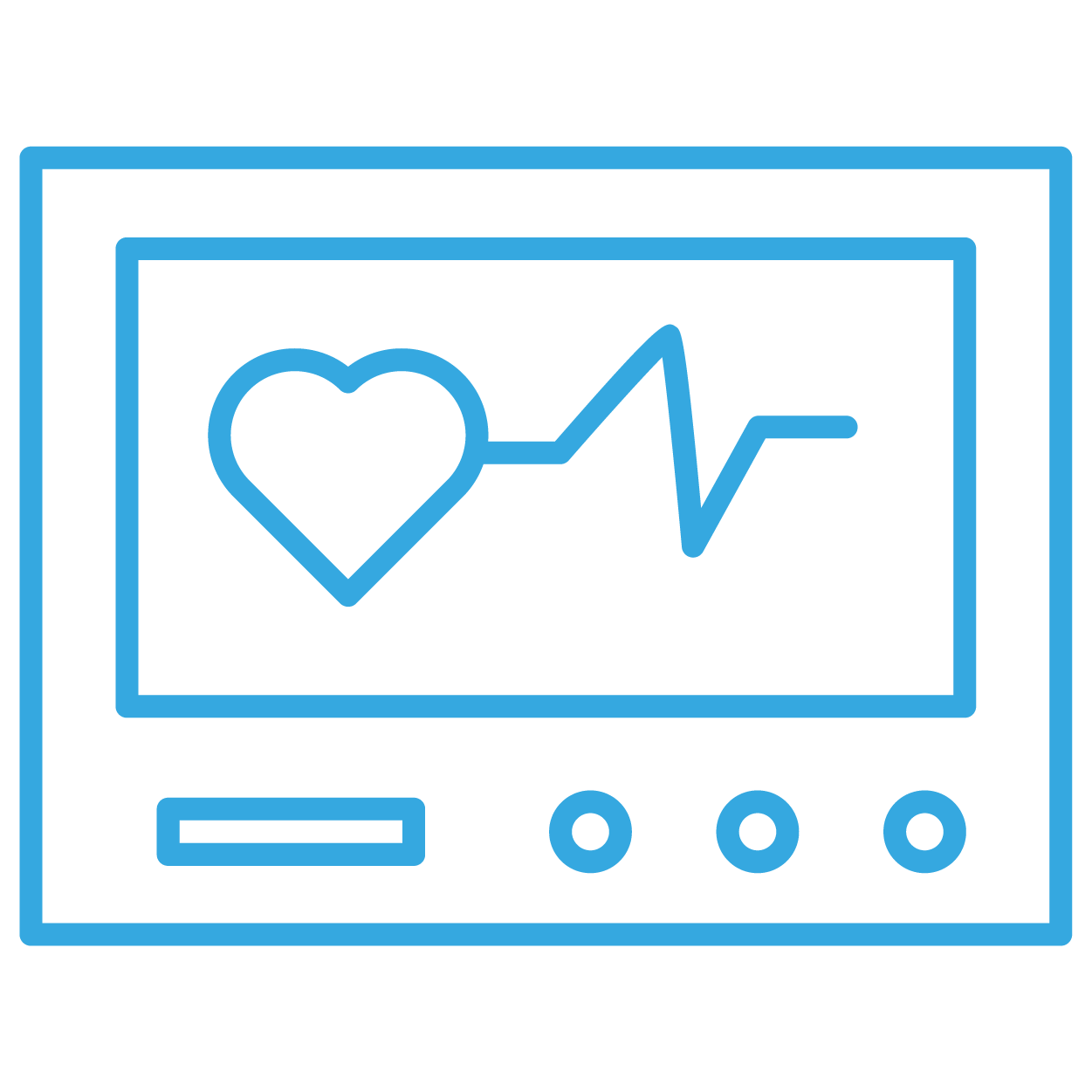
Fibers and coatings
Fibers and coatings
Each format is engineered with precise control over fiber alignment, porosity,
mechanical properties, and degradation kinetics—critical parameters that influence clinical performance.
Finished Product Manufacturing
Semi-finished materials are then integrated into finished medical devices, often in cleanroom ISO 5/ISO 7 environments. Key processes include:
Shaping and molding
of membranes, patches, or implants
Crosslinking
to adjust bioresorption rates when required
Sterilization
(e.g., gamma irradiation or ethylene oxide) validated to preserve collagen’s bioactivity
Packaging and labeling
in compliance with CE and FDA regulations
At every stage, we perform comprehensive quality testing—including molecular integrity assays, biocompatibility testing, and mechanical performance evaluation—to ensure that the final product meets the exacting standards required for use in regenerative medicine and medical aesthetics.